May 16, 2016. Ovc alarm on fanuc robot keyword after analyzing the system lists the list of keywords related and the list of websites with related content, in addition you can see which keywords most interested customers on the this website. Keyword Suggestions Most Searched Keywords. Easy mah jongg rules 2.
•Simulation of FANUC robot commands •Highly accurate simulation •Download program to robot Robot motion confirmation. Estimate OVC, OH alarm by motor torque. Dec 18, 2012 If yes, the robot moved a bit during shipping, not a big deal. Go to sysvars DMR_group and set 'master_done' to True Go to the master-cal screen ('type'menu) and hit res-pca soft key and then select 6 for Calibrate. If the technical data of the robot such as duty cycle or load weight is higher than the rating. Check the line voltage. (33) SRVO-046 SVAL2 OVC alarm (Group: i Axis: j) o (Explanation) This alarm is issued to prevent the motor from thermal damage that might occur when the root meant square current calculated within the servo system is out of. Apr 14, 2013 The problem is that OVC is generated only when the robot is run at low speed and at only one point in its path. There is no problem when the robot runs during production i.e., 100%. The OVC alarm is generated in the 5th axis (only) and at only 1 point in the cycle where the current in the J5 axis (-21.8 A) is almost close to the.
Most common alarm requirements found by Fix Zone experts during repair. When your CNC device suddenly prevents operating what is usually the first factor that you do? Probably open the cupboard and check the controller or amplifier? If your machine is equipped with Fanuc Automation parts, you probably verify the position display on your Fanuc servo amp and notice a amount shown? These figures are called alarm requirements, or mistake rules. There could be 9 possibilities.
The push and amp experts at Fix Zone make use of these alarm requirements, also known as fault requirements, to assist them troubleshoot during a maintenance. When, many periods our specialists see the same fault requirements come up. Here is a listing of the nearly all common Alarm codes discovered on the position screen on C-Séries, Fanuc servo ampIifiers: Security alarm Code #1 Overvoltage alarm (HV). If DC voltage of main power source is abnormally high, overvoltage sensors takes place (HV level: 430V DC).
Alarm takes place when regenerative discharge resistor is certainly disconnected. For 200V Air cooling input, primary signal voltage is certainly 283V DC (200 back button 1.414). Discharge operation is began at voltage of primary signal voltage plus 60V.
Security alarm Code #3 DC hyperlink undervoltage alarm (LVDC). Alarm happens if DC voltage of major circuit power supply can be abnormally reduced (LVDV level: 120V).Causes may consist of power source voltage (+15V) becoming 10Vor lower and driver module PCB not inserted usually. Alarm Program code #8 Overcurrent alarm (HCL). Security alarm happens when unusually high present runs in major signal of 1-axis amplifier or in major routine of M axis of 2-axis amplifier.Causes may consist of faulty IC, unusual PWM transmission, and grounded wires. Alarm Program code #2 Control strength supply undervoltage alarm (LV5Sixth is v). Security alarm happens if control circuit strength source voltage (+5V) can be abnormally reduced (LV5V degree: 4.6VDC). Alarm Code #5 Extreme regenerative release alarm (DCOH).
Security alarm takes place when average regenerative release energy can be too high.Leads to may consist of procedure of thermostat for regenerative release resistor or thérmostat between (15) and (16) on port block Capital t1; this procedure outcomes from too frequent acceleration/deceleration operations. If you have any queries or require assistance, make sure you contact 989-922-0043. To view our Fanuc Amplifiers in stock and fix features at RepairZone, click on here: Various other Related Blog Articles:. Related Videos: Follow RepairZone ón Linked In: Please talk about our Articles. Author:. 37 Comments. Nimer I wont to understand the servo aIarm un the machine.
safwat Thank you My device write code 8 and l reed what this mean to say but I dont know what I do Please help me what I perform. author Hi there Safwat, Give thanks to you for your issue.
Alarm code 8 is usually a L-áxis over-current aIarm(HCL). This aIarm happens if an abnormally high present flows in the L-axis engine. If you meg the motor and the wire and they are good, then it is definitely probably out of spec parts on your travel and it will possess to become repaired. Regards, Jade Yórk.
Russell Thompson Whát will status d on my servo amplifier mean and how would i correct it Thanks RusseIl. Scott Lindsey Hello. The amplifier (Air conditioners SERVO Amplifier C collection) has a 3 on the status. This amp the servo electric motor has long been transformed out approx. Whát else should l be looking for?.
Motn 017 Limit Error Fanuc
writer Hi there Scott, Sorry I skipped your query. This may tone funny but many times individuals wear't engage the breaker switch on the top of the travel. Other cases point to a bad wire from the motor to the travel. Regards, Jade York. Joe Good morning. I possess a old 2 Capital t fanuc controller and after the material crammed I got a alarm 00172 I tried placing all overloads but no response from the device, fast and give food to work but no turn or collet closing.
Thanks a lot joe. Martin Hérnandez Rios I have got a CNC Milling Device and I wear't find the origins of this Alarm code in the Guide. The Security alarm 60M5-04, anybody who can help me make sure you. Item: V-CNC 500 Design: EKT Serial: 7085-f00-KH0020 Cinaninnati Milacron INOVA Company Thank's in progress. I'michael in South america ( Juarez,Chihuahua MX ). writer Hello Martin, However, I could not really find any information on this.
You should seek advice from with Cincinnati MiIacron OEM for help. Regards, Jade York. Saurabh Tyagi My cnc device is give the massage over voItage in DC-bus/DC link(fo2) so how to solve this issue It can be bottero cnc. writer Hello there Saurabh, Many instances when you obtain a over-voltage, it is definitely triggered by either the servo engine or the IGBT is certainly poor in your strength supply. To become more accurate, I would need the producer and design quantity of the commute.
Regards, Jade Yórk. abdelmged fathi lord evening i actually have Security alarm Code 3 type/A06B-6066-H244 energy offer voltage (+15V) Can be OK. author Hello, Make certain the breaker switch is certainly in the ‘on' placement on the best of the drive. This should resolve your issue.
Please allow me understand if I can assist further. Regards, Jade Yórk. Jagdeep 0hlan My device servo amplifier A06B-6079-L204 A and shows alarm 2 in position in morning hours when device starts after 3 hrs. Off owing to change switch.
In day time it not shows any alarm. Can be this is drive handle PCB associated alarm and handle card require to fix. Please suggest via email id. author Hello there Jagdeep, #2 alarm indicates the travel is not getting low control voltage.
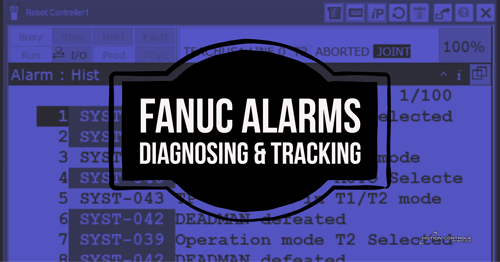
When alarm happens, verify for 24vdc at CX2A new. If good then push has elements out of spec causing the alarm. The travel will have to be evaluated. If it is definitely not getting 24vdc, then your problem can be your strength supply or cable connection.
You can deliver the commute or energy source, whichever is usually malfunctioning, to us at Maintenance Area for a free assessment: Maintenance Zone 615 Andre Road Bay Town, MI 48706 Ph.(989)922-0043 Allow me understand how I can assist further. Regards, Jade Yórk. anggriyan My fánuc showing #5. Error what can i do, i already alter all three pcb and transformation power supply dc and the voltage is oke but nevertheless displaying #5.
writer Hi there Anggriyan, The consumer states the DC voltage is definitely great at the get which indicates there is usually an inner problem in the push itself. The Drive will possess to end up being sent in for evaluation and restoration.
We would become joyful to evaluate it for you for free! You can ship it to: Maintenance Zone 615 Andre Road Bay City, MI 48706 Respect, Jade York. George Hi We have an injection molding device. The robot motion is controlled by fanuc servo unit.
When robot power is on, it shows ‘0' web browser prepared but when we attempted to proceed the robot it displays not prepared ‘ - ‘ sign. The device HMI shows alarms. Common Servo mistake 2. Automatic robot contoller, amp or engine alarm. Could you make sure you help.
author Hello there George, Your issue may end up being the motor, or it could end up being a cable, or the amplifier. You can usually thin it down tó one of thém by swapping out parts and attempting them in a different axis. Once you find what isn'capital t functioning, you can deliver it in to get verified and evaluated. Repair Zone will perform it free of charge of charge, and provide a fix quote. Let us understand and we can support you. Regards, Jadé York. George Hi there We have got a Fanuc power mate L and there a Directed indication S i90001,H0,WD and EN.
The S1 Red is crimson now. What that indicator means. Could you please help us. writer Hi George, Thanks a lot for your issue. From where I feel standing, most most likely it is a link/communication problem.
Check (JS1A tó JS1) ánd (JX1M jumper or link to next drive). I hope this functions for you. Make sure you allow us know if it will, we'd like to hear back again! Regards, Jade Yórk.
andrawes saIman hi déar my machine give me (8.) alarm can you help me what i can do. author Hi there Andrawes, Thanks for your issue today. The #8 fault is abnormally high current runs in the L-axis engine, a very common mistake.
As long as the cables and electric motor tests good, you can separate the 8 fault to getting a blown IGBT or some other bad elements on the A06B-6079-H106 Fanuc amplifier. A alternative would end up being to send out it in to Maintenance Zone for a free assessment and quotation for maintenance. Repair Area has seen many of these models in for maintenance through the yrs and offers had great achievement! Or (989)922-0043 Best Regards, Jade Yórk.
adam schnurr Have got an a06b-6111-h030#570 with an alarm program code 15. I know its not really my ladder we have been running this machune for 10 years. With no problems. How do I shape out if its the permanent magnetic get in touch with or the I/o unit. author Hi there Adam, Thanks for your issue. The best issue to do is move over the following steps: Alarm code 15 In result switching control or spindle turning control, the changing operation series was not executed properly.
Spongebob squarepants season 3 torrent. You can use it on any Mac running Mac OS X 10.6.x or EARLIER. Internet explorer for mac download 2016. Running it on a Mac was a challenge, that is until Microsoft released IE 5 for Mac. Internet Explorer 5 for Mac uses a rendering engine called Tasman. You did it because it was the best browser around or because you used it on a Windows box at work, and running it at home was a no brainer. Internet Explorer 5 is the latest version of its flagship browser that Microsoft developed exclusively for Mac users.
This alarm is usually issued if one second or more elapses from the transition of a switch request transmission (SPSL ór RSL) until á power line state check signal (MCFN, MFNHG, RCH, ór RCHHG) makes a changeover. Troubleshooting when this alarm is certainly issued (a) The permanent magnet contactor (switch unit) for strength line switching is usually faulty. If the contact is definitely inoperative, verify the energy source of the permanent magnet contactor. If the permanent magnet contactor is still inoperative, replace the permanent magnetic contactor.
(t) The I/U device or wires for checking out the contact of the permanent magnetic contactor is definitely faulty. If a defect is discovered in the We/O device or wiring, substitute the I/O unit or wiring.
(c) The sequence (ladder) can be wrong. Modify the sequence so that switching is finished within 1 2nd. Let us understand if I can assist further. If you need professional assistance on the device, we can assist. Proceed to and get your repair started. Truly, Jade York. Carl Hello, I possess alarm #2 on my Fanuc servo amplifier (A06B 6079 H206) when the major power can be first changed on in the morning.
If I keep the power on for about 30 securities and exchange commission's switch the main strength off after that on after a few seconds the alarm goes away. Can be there probably a battery power going bad in or is usually the amp probably on is method out. The backup encoder position batteries on the cabinet door are usually good. Thanks a lot. author Hi Carl, To respond to your issue about the #2 alarm on your A new06B-6079-H206, if there will be approximately 24vdc at the CX2A new connector after that the commute has parts out of spec and will need to end up being refurbished. We can definitely assist you with that.
Move to and get your maintenance started. Good fortune to you and I wish we can help! Truly, Jade York. Lowell Kenney Great Evening, We have got a 2000 Takisawa Former mate-108 with a Fanuc 21i-Testosterone levels control, that I would like to get back into creation. It has an error code #24 on the Spindle Amp, the publication states that it can be a communication error so have long been searching for bad cable connections or damaged wires. Therefore far nothing at all.
Any recommendations would be appreciated. Lowell Kenney. author Hello Lowell, Thanks for reading The Machine Runner Blog! AL-24 can be a conversation error to Spindle connector JA7B. If there is certainly a brand-new or recognized good cable in location then changing out spindle amplifiers would be the next phase. (If extra is available.) Some age or out of spec elements in the Spindle amp can result in alerts.
The Amplifier can become delivered in for an assessment. Our site, is certainly the portal to our nationwide repair solutions. We would become content to help with an assessment of your Fanuc amp, if necessary. I hope this info was of some value to you. Thanks again, Jade York. Ivan Hi there. On my Wire cutting machine (robofil 440slp) i possess a problem with Fanuc PSM model A06B-6114-H303(it is usually alpha i SV 20/20/20).
Fanuc Soft Thermal (ovc) Alarm
On the display will be the letter G and the two some other SVM will not energize (there is usually a series in the middle). Perform you have got any recommendations for me make sure you. Best regards Ivan.
author Hello Ivan, Thanks for your remark today. The letter P is a conversation mistake between amp and module. Check all of your connections, cable fór CXA2A tó CXA2B can end up being faulty. I hope you can solve this problem. If you require further assistance, you can send out your Alpha i amp in for assessment: Regards, Jade Yórk. MARCO Hello, Wé have FANUC ROBOCUT with 18i, 5 axes cnc.
We have alarm #9. This alarm occured when normal temp. In machine cabinet is usually 100-104 Y. (Sizzling summer and we have not surroundings fitness ). When is usually about 68 N, this alarm not really occurs. author Hi Marco, Thanks a lot for your issue today.
Right here are a couple of options. The M or (Y) axis IGBT is usually weakened or amplifier elements are faltering under the high temperatures. The Enthusiast must end up being functioning effectively without as well much contamination. The amp may end up being expected for reconditioning. Sending your amplifier in to a reliable, cost-effective supply like Fix Zone can get things operating smoothly again. Here is definitely a hyperlink to obtain you started with a free of charge assessment: I hope this assists! Best Regards, Jade Yórk.
Daniel Kerley l have an old fanuc managed machining center. I have always been obtaining alarm 56. I found that the fan was broken and so I replaced it. The new fan is definitely operating completely but I have always been still obtaining the alarm 56. author Hi Daniel, Thanks for getting in touch with us with your question.
Security alarm 56 is an inner cooling fan halt. The smaller sized fan situated inside the yellowish case can be the lover that must end up being changed. If that was changed and there is certainly still a fault, then there could be components out of specification, trace harm, or other issues. Best 16tb external hard drive. If you require further assistance, you can send out your device in to Repair Zone for a free of charge evaluation.
Repair Slip: Best Relation, Jade York Fix Zone. Pete Schneider Hi. No opinion but a optimistic query. I possess a fanuc turret spindle commute with a #12 alarm that will not really clear with pwr. Down and back up. I wish that you can tell me about the alarm. writer Hello there Pete, Thanks for your question.
#12 alarm program code is most likely an IGBT offers a short. This would require changing shorted IGBT with a brand-new one. If this is definitely something that you require a assist with, you can send it to Repair Zone for a free of charge assessment and quotation. You can start your repair here: If you have got another issue, just allow us know. Greatest Regards, Jade York.
Contents. Common questions. Run Plan. Switch on FANUC. Switch the key to Auto mode on Robot. Shift the change on the Training Necklace (TP) to OFF.
Press Select on thé TP and scroIl down to thé appropriate communication system. (LABVIEWCOM, LVCOMFRM, etc.).
Press Enter. Strike Reset to zero to clean any Problems (Red LED on). Hit the green Start switch on the Fanuc controller. Light should change on Green. If it doesn't, then examine for errors.
Elgato sound capture mac download. Automatic robot will shift to it's House position.
Hp image viewer download. Robot systems include a variety of equipment to keep operators/people safe around an active robot cell.
Some of these physical safety devices include:
- EMERGENCY STOP buttons
- Safety fences, barriers, or chains
- Light curtains
- Interlocks
- Pressure mats
- Floor directional and safety markings
- Warning lights
- Mechanical stops
Dual Check Safety (DCS) is a software used to program safety features in the robot system using built-in sensors. DCS limits the robot workspace and speed to a defined workarea. Then DCS monitors these established parameters stopping robot motion if the robot moves beyond any parameter and triggering a DCS Alarm.
If the robot does reach outside the established safe zone the alarm can only be cleared using the teach pendant in T1 mode to move the robot back into the safe zone.
Watch Step by Step Robot How-to Video for Resetting a DCS Alarm
Types of Stops (following IEC 60204-1)
- Power-Off Stop– Servo power is cut, and the robot stops immediately. This occurs when a collision is detected – this type of stop should be analyzed to make sure it is preventable in the future because immediate stops are bad for the overall robot health.
- Controlled Stop – typical stop where speed is slowed as robot stops (yet robot stays inside the safe zone) then servo power is turned off.
- Smooth stop – This stop is like above, but robot is stopped quicker.
- Hold – The robot is slowed to a stop but the servos remain on and the robot can continue without clearing an alarm.
DCS is also used to keep the robot arm and tooling away from other mechanical items in the robot cell, like conveyors, product, other stations.
The DCS menu on the Teach pendant is where these parameters are set up, and anytime there are any changes to the cell the setup should also be adjusted.
- Joint Position Check – checks to make sure the robot joints are within the defined safety zone
- Joint Speed Check – checks to ensure the robot speed remains in the safe limit
- Cartesian Position Check – Establishes a safe zone and checks orientation (yaw, pitch, rotation – W,P,R)
- Cartesian Speed Check – checks TCP (Tool Center Point Control) speed
- T1 Mode Speed Check – Monitors the TCP or Face Plate speed shutting down the motor power if it ever exceeds 250 mm/sec
- User Model – helps build the shape model – defines robot and tool shape
- Tool Frame – Allows input of different size items that may be picked by the tool
- User Frame – Based on (x,y,z,w,p,r) coordinates
- Stop Position Prediction – Predicts the stopping position of the robot based on robot, payload, and speed
- Robot Setup – selection of which robot is in the robot cell
- Mastering Parameters
- /Speed Check Setup
- Safe I/O Consistency Check
- Safe I/O Device
- Signature Number
- Code Number Setup
Instructions to Reset a DCS Alarm
Fanuc Servo 046 Ovc Alarm
If the robot does reach outside the established safe zone the alarm can only be cleared using the teach pendant in T1 mode to move the robot back into the safe zone.
Dual Check Safety is a software used to define the robot's workspace and speed. DCS monitors robot motion stopping the robot if it moves beyond any set parameter and triggering a system alarm.
- The robot needs to be in T1 for a DCS reset procedure and the Teach Pendant needs to be ON
- Select MENU and arrow down to ALARM – The alarm screen shows a SRVO-402. This is a DCS alarm saying that the Cartesian Position is out of limits.
- Now select MENU and arrow up to NEXT and press ENTER – This brings up MENU2 – arrow down to SYSTEM and ENTER
- The System Clock screen is visible. Now go down to the Menu bar and select | TYPE |and Arrow to DCS
- The DCS screen shows a list of DCS parameters and the Cartesian Position Check parameter is marked as Unsafe
- Right Scroll > the lower bar menu until you see 4D. A model of the robot pops up on the right side of the screen. You can see that the zone is red meaning the robot can not move.
- Select SHIFT and RESET –Then select SHIFT again – In this example we are in WORLD jog mode and the robot has gone out of the zone in the + or – Y direction, so to get back into the zone we will jog using the + or – Y jog key. For your specific DCS error use the proper jog keys on the right of the teach pendant.
- The alarm that was present on the top of the teach pendant is gone and the robot is now in the green, safe zone and can continue working.
Some have called bin picking the 'holy grail' of robotic automation and it certainly is…
Robot System Cost Series Part One: 10 Parameters Part Two: The Range of Robot Cost…
I had spent long enough analyzing prices at the local big box store for grass…
Area Scanners When there is a moving robot, equipment or machinery in a system, it…
In this Tech Talk How to Robot Series article we are going to go through…
Fanuc 436 Soft Thermal Alarm
DCS Part two (read part one) - How Could This Lead To A Fenceless Robot…
In-depth experience and flexible system design make Motion Controls Robotics' robotic roll handling systems something…
Srvo 046
PRESS RELEASE December 17, 2019 Fremont, OH - Motion Controls Robotics, Inc (MCRI) is excited…